Type your username and password then click on the appropriate section you wish to access.
Click here if your login fails (might occur on certain Apple products)
news
Phoenix Reisen goes green with engine retrofit to meet the highest environmental standards
Wabtec Corporation (previously GE Transportation), has been first to launch a medium-speed marine diesel engine series, L250 and V250, certified to meet the strictest emissions standards of IMO III and EPA Tier 4 by deploying advanced EGR technology.
By September 2021 two of these gensets will be delivered and installed aboard the MS Amadea, the flag ship of Phoenix Reisen, which is well known to the German tv audience from the ZDF tv series “Das Traumschiff”.
VMS Group emphasizes the company’s strong position as an efficient and reliable supplier of total marine solutions in the demanding and quality-conscious cruise industry. In the retrofitting of MS Amadea all VMS Group’s competencies are drawn upon – ranging from sales and project planning, design and engineering services as well as the technical calculations of vibrations and noise levels to the actual assembly and load testing of the new gensets before installation on board.
“This is where the synergy of our many competencies really comes into play, and our highly experienced engineering team has worked hard to find the most optimal solution”, says Kim Rasmussen, VP Project Sales at VMS Group.
Optimized IMO III certified diesel gensets
“We are proud to partner with VMS Group to power the Phoenix Reisen fleet. VMS Group’s development and design of these gensets is impressive and a great fit for our engines. The gensets are optimized in a way that minimizes both noise and vibration while being certified to IMO III emission levels without SCR and urea injection, and this will clearly attract even the most demanding projects,” says Rob Van Solingen, European Sales Director – Marine and Stationary Power, at Wabtec. In addition to VMS Group, the independent ship design company C-Job Naval Architects will provide the technical management in corporation with technical management by BSM Cruise Services for the full conversion project of MS Amadea, which currently is in the port of Bremerhaven due to the corona pandemic, but has a busy summer schedule planned, cruising the Mediterranean Sea and the Norwegian fjords.
Takes a lead
“In a time where most cruise companies are in heavily strain due to the corona pandemic, it speaks in the honour of Phoenix Reisen to make the decision to enhance their fleet by the retrofitting of the MS Amadea”, says Bosse Berg, Technical Superintendent at Bernhard Schulte Shipmanagement (BSM) Cruise Services, the German company managing the vessel on behalf of Phoenix Reisen. “As a responsible travel agency with more than 30 years of experience within the cruise industry we aim to set the highest standards. Standards, to which the engine from Wabtec is not only pioneering but also takes a clear lead”, says Johannes Zurnieden, founder and CEO of Phoenix Reisen.
No urea saves space
A common methodology used to meet the IMO III or EPA Tier 4 NOx standards is reducing NOx in the exhaust gas through deploying a Selective Catalytic Reduction (SCR) exhaust gas after-treatment system and urea injection.
The SCR after-treatment technology requires provisions for space and weight for urea tanks, dosing pumps, piping, a mixing tube and the SCR reactor. Other disadvantages of urea based after-treatment systems include the complications associated with handling urea on board the ship, controlling ammonia slip, the incremental operational cost for consuming urea, and additional maintenance scope.
An alternative methodology to meet the IMO III or EPA Tier 4 standards is to limit the formation of NOx in-cylinder through deploying Exhaust Gas Recirculation (EGR) technology.
The Wabtec series L250 and V250 are based on this EGR technology, which minimizes the formation of NOx during combustion as opposed to reducing NOx in the exhaust gas through a series of chemical reactions in an after-treatment system.
Significant benefits
Engines with EGR technology offer significant benefits over engines with SCR after-treatment technology such as lower system weight, lower installation cost, lower operating expenses and the requirement of up to 40 % less space.
Since commencing commercial production in 2015, the technology has been successfully rolled out with over 100 units delivered solely for marine applications, having accumulated over 600,000 operating hours.
The references include several expedition cruise vessels and, among others, ferries, offshore support vessels, dredgers, polar class research vessels, tugs, ATB tugs and push boats.
At the 2018 Lloyd’s List Americas Awards the breakthrough EGR technology won “Best Technology for Cleaner Emissions” category.
Meeting green demands
The requests for greener, more sustainable and environmentally friendly solutions are rapidly growing, also in the cruise industry, and more companies are expected to follow in the slipstream of Phoenix Reisen.
Facts:
· VMS Group covers a wide range of competencies, sales and services within the maritime and offshore industries.
· The company is headquartered in Frederikshavn with subsidiaries in Brazil and Namibia.
· The core services include: Repair and maintenance of gear, propeller and diesel engines. Repair, maintenance and balancing of turbochargers for marine engines. Sale of spare parts, motors and gears. Ship design and project management.
· VMS Group’s distributorship for Wabtec Corporation’s L250 and V250 diesel engines covers the Scandinavian, German and Brazilian markets.
· The Wabtec L250 and V250 marine diesel engines meet the stringent environmental requirements of the EPA Tier 4 and IMO III regulations from respectively Environmental Protection Agency, EPA, and the International Maritime Organization, IMO.
· The technology behind the engine eliminates the need for a Selective Catalytic Reduction (SCR) system – thus making it unnecessary to store or use urea on board, freeing both cargo and tank capacity and saving all the expenses associated with purchase, installation and maintenance of this extra equipment.
· The combination of no SCR, no dosing and monitoring equipment or urea tanks can save up to 40 percent space and reduces the complexity of the ship design and yard installation time and costs.
-
Kim Rasmussen
Vice President - Project Sales
+45 2177 1810
kr@vms.dk
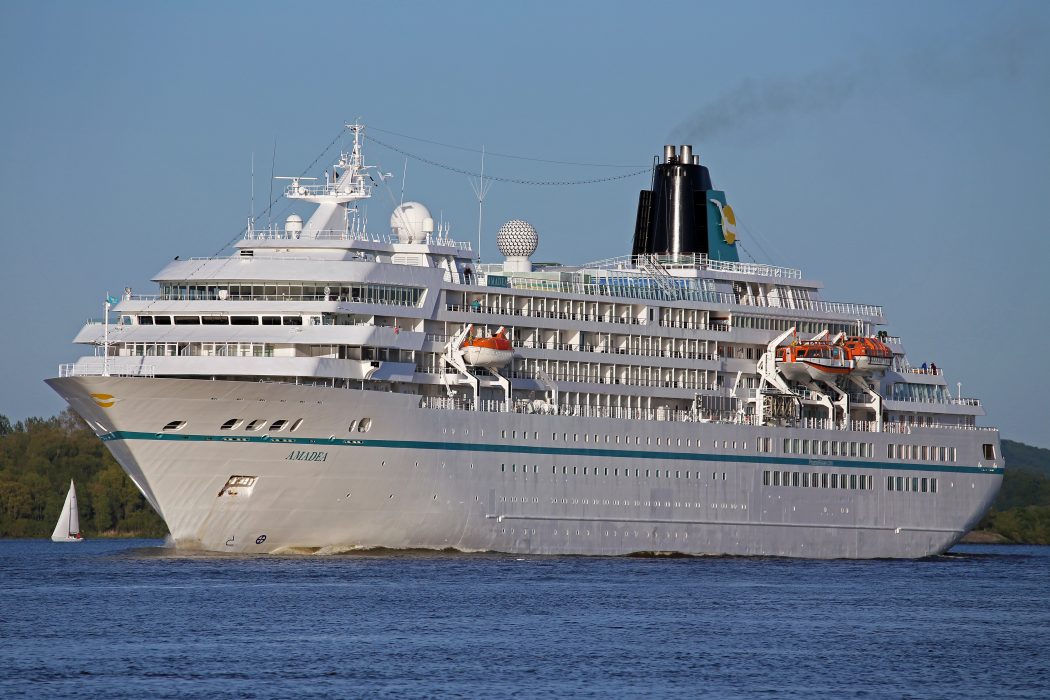